The race to standardize plant knowledge from programmable logic controllers (PLC), sensors and manufacturing strains is occurring quick. As meals producers standardize knowledge, digital instruments speed up and supply a more in-depth have a look at total tools effectiveness (OEE) and upkeep metrics.
Meals manufacturing is the biggest employer amongst manufacturing industries, using greater than 1.7 million staff. Nevertheless, labor shortages within the meals phase have been properly documented and at present sit the place employment was in 2017 and 2018. With many meals vegetation reporting capability utilization, any shocks to labor availability will add extra challenges to plant managers and company basic managers.
As proven, the final 10 years have been difficult hiring and retaining certified plant staff. Meals firms have responded to those challenges by investing in superior expertise and shifting towards extra automation. Current surveys level to extra capital expenditures for predictive upkeep, with many company initiatives executing knowledge standardization.
In a latest PMMI survey, meals business personnel have been requested how they have been leveraging expertise to treatment any data or expertise hole of their operations. Integrating sensible expertise to help operations and upkeep took the highest spot at 44%. The next two spots included automating via massive language fashions (LLMs) at 38% and standardization at 31%.
Meals operations are discovering elevated throughput and troubleshooting line faults on account of new digital instruments or middleware expertise. Within the course of, firms are fixing bottlenecks quicker on account of manufacturing line and PLC knowledge standardization.
“Meals and beverage firms with a number of vegetation are more and more looking for Manufacturing Execution Programs (MES),” says John Oskin, senior vp at SmartSights. “When implementing MES, there’s a sturdy agenda to standardize knowledge.”
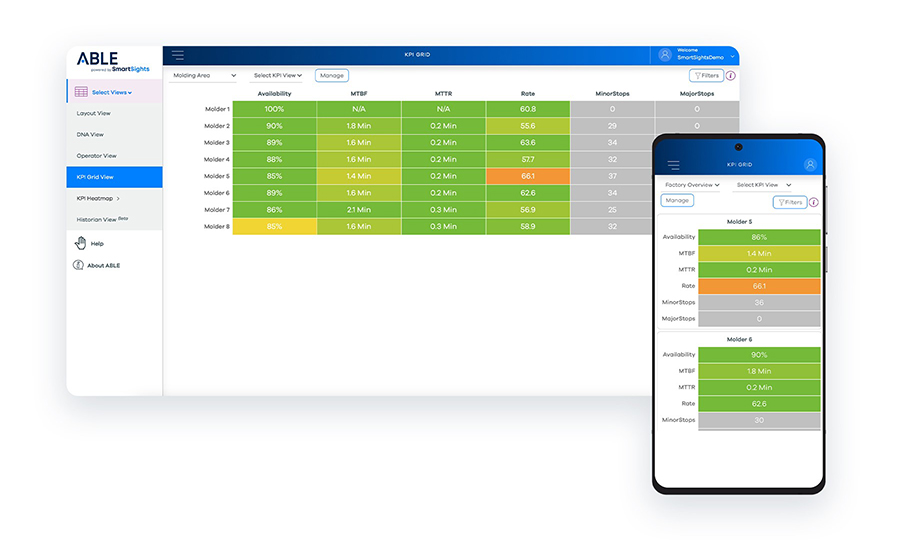
Standardizing Information for Trusted OEE
Trade 4.0’s promise is to attach plant flooring manufacturing to middleware, and ultimately, to an ERP system. However that’s predicated on clear and standardized knowledge.
“Once we began MontBlancAI two-and-a-half years in the past, we had this naive view that producers had good knowledge sources since machines are glorious knowledge sources,” says Markus Guerster, founder and CEO, MontBlancAI. “We realized that the info sources are nice, however the expertise that collects, cleans and shops the machine info isn’t good at dealing with vital knowledge quantity.” MontBlancAI machine-learning AI answer depends on actionable knowledge from PLCs and sensors.
“Whereas there was a concentrate on upkeep metrics, particularly OEE, there was no standardized approach to measure throughout the enterprise,” provides Ravishankar Subramanyan, HiveMQ director of business options manufacturing. “This could lead to firms having many variations of the OEE, which is tough to match and distinction.”
“Ten years in the past, OEE methods have been monitoring on the bottleneck, and it was a very good technique, however right now that isn’t satisfactory for AI or taking OEE to the following stage,” Oskin says. “It’s tough to offer correct root trigger when solely wanting on the bottleneck asset, so this necessitates the necessity for superior knowledge assortment.” SmartSights’ expertise offers a low code/no code software that enables meals and beverage producers to offer clever root trigger with out PLC programming.
“Now we have an strategy that may mix PLC packages and HMI configuration recordsdata, to determine key items of data for MES and OEE purposes. This info is then unified and packaged for fast deployment.” Oskin says. “Getting constant PLC knowledge assortment is achieved utilizing our templates and adopting requirements resembling PackML.”
With continued mergers and acquisitions of recent vegetation within the meals phase, standardizing OEE and different metrics — imply time between failures (MTBF), imply time to restore (MTTR), asset availability and deliberate upkeep proportion (PMP) — has been a tough problem, however massive system software program and knowledge standardization are serving to.
HiveMQ affords a Message Queuing Telemetry Transport (MQTT) platform that connects manufacturing knowledge all through the corporate. “One of many methods for capturing and standardizing OEE, MTBF, throughput, yield and effectivity metrics is making a Unified Namespace,” Subramanyan says. The corporate pushes a Unified Namespace for sensors, controllers and tools, which embody downtime occasions, cycles instances, power consumption and defects.
For HiveMQ, setting up these fashions entails unifying knowledge from a number of sources and creating a knowledge mannequin for downtime:
- Machine or PLC knowledge indicating when downtime begins and ends
- Guide or automated cause codes for the downtime
- Operator and shift info
- Bodily location of the machine
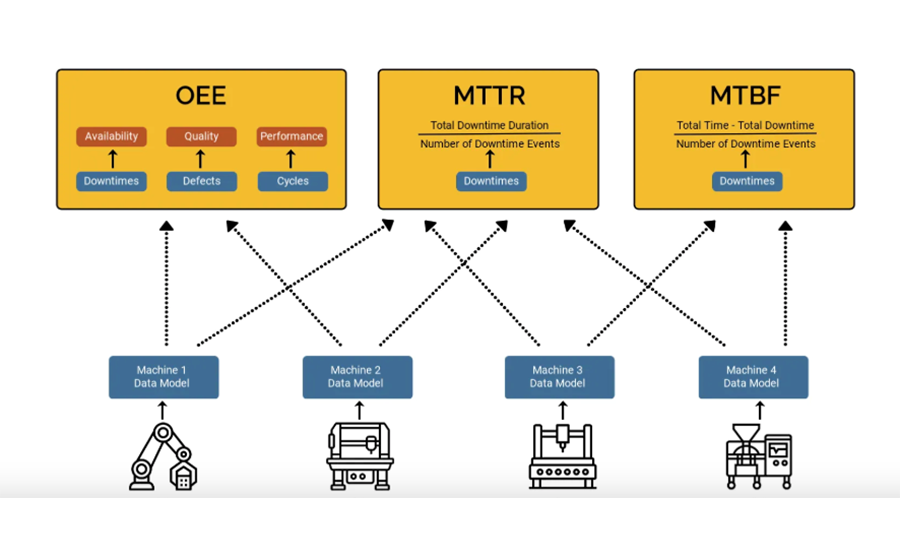
MQTT is getting used more and more as a knowledge protocol with Supervisory Management and Information Acquisition (SCADA) platforms. At a latest Ignition Convention, Shamrock Meals’ Alec Gordon, lead controls engineer, confirmed how the corporate collects motor knowledge and makes use of it to alert upkeep personnel of a doubtlessly failing asset. Shamrock Meals makes use of Inductive Automation’s Ignition SCADA platform for its vegetation. With the help of the SCADA platform, Gordon developed person interfaces for Shamrock Meals Firm’s upkeep group, together with a Variable Frequency Drive (VFD) monitoring display, a drive motor display to help with predictive upkeep and a scanner diagnostics display.
“Our upkeep group was having a lot hassle diagnosing VFD faults. It was extra of a coaching challenge, however we additionally wished to offer them with plenty of VFD diagnostic info wherever they ran,” Gordon mentioned throughout his presentation.
Gordon provides, “So after we outlined our Ignition setup, we used a naming conference for Open Platform Communications (OPC) PLC connections, which outlined Person Outlined Varieties (UDTs) and employed a multi-instance wizard to outline all the pieces uniformly, after which making use of our historian.” The unified UDTs create tags for every VFD after which are linked to an information historian from Canary Labs.
Canary Labs historians concentrate on optimizing and studying time-series knowledge, performing calculations on knowledge units despatched to them, after which transferring that knowledge again into Ignition publishing through MQTT. With using standardized knowledge tags within the SCADA platform, Shamrock Meals runs calculations on all 382 VFD property without delay, resembling p.c property.
“I did it over 45 days since I figured that’d be a ok snapshot of an asset’s common,” Gordon provides. “If it began to fail for 3 days, let’s say you would possibly see some spikes and it might throw off your common, however doing a development over 45 days ought to be sufficient to filter that out and offer you a reasonably correct amp.”
Extra Good Know-how for Upkeep
Varied digital instruments are rising for meals firms in upkeep and operations. For instance, smaller digital twin device purposes are being employed for upkeep to simulate manufacturing sequences to offer a extra correct evaluation of downtime causes.
“We’re capturing uptime, downtime, throughput and reject info accounting for each minute of the day and might synchronize that knowledge throughout a bunch of property on the road and even throughout strains,” Oskin says.
The digital twin performance permits a upkeep group to replay and validate the info. “From a plant perspective, many issues occur off shift or on third shift, when there’s not lots of people round,” Oskin provides. “So, the flexibility to replay this knowledge permits them to see a sequence of downtime that may’ve led to a crash.”